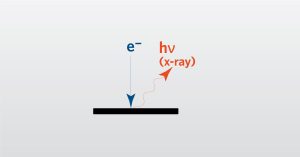
SEM-EDS Webinar
In this webinar we will focus on Energy Dispersive X-ray Spectroscopy (EDS) and Scanning Electron Microscopy (SEM)
Home » Amorphous vs. Crystalline Materials
As new products are developed, appropriate materials are selected based on the end-use of that product. The type of materials used can affect functionality, productivity, and lifetime. Solids fall under two main categories: amorphous and crystalline. These two types of solids have different properties that may be more beneficial for certain products or applications.
When comparing amorphous and crystalline solids, the main difference in the material is the atomic structure. Simply put, crystalline solids have a repeating atomic structure, extending over distances much bigger than the interatomic scale, while amorphous solids do not.
In crystalline solids, the regular repeating atomic structure creates a distinct diffraction pattern when exposed to an incident X-ray beam. They are also harder than amorphous solids and have set (or narrow) melting and freezing points. A good example would be diamonds and graphite. They are both made up of only carbon atoms, but the structures they have are completely different, which dictates their material properties.
Amorphous solids are typically softer and will not produce a diffraction pattern. Instead of a set melting point, there is a temperature range and the densities of amorphous solids are typically lower than their crystalline counterparts. Glass, some polymers and rubber are examples of amorphous solids. Sometimes it’s not readily apparent what type of material you may have. This is where Eurofins EAG can help.
X-ray diffraction (XRD) is a powerful non-destructive technique for characterizing crystalline materials. Eurofins EAG uses XRD to provide information on phase identification (ID), semi quantitative analysis, and percent crystallinity of your material. For many years, we’ve used this analysis on all types of materials, including semiconductors thin films, ceramics, metals, carbon for battery anodes, pharmaceuticals and much more.
For phase ID, we use the diffraction pattern as a fingerprint of the crystalline sample. We have access to a database of reference crystal structures that we compare to our experimental data to find a match and determine the most likely phase.
In semi quantitative analysis, we can refine a pattern to determine weight fractions of your compound. XRD analysis can also calculate the percent of crystalline vs amorphous solids in your material. In some cases, one may be preferred over the other based on the end-product or industry.
In the pharmaceutical industry, the formulation and molecular structure of a drug is critical and can affect how it reacts with your body. If the chemicals are properly formulated but the drug has the wrong structure, it could have major health and safety problems. At Eurofins EAG, we can help identify these structures.
With our wide range of services, we offer complementary techniques to tailor to your needs. X-Ray Fluorescence (XRF) is another non-destructive technique that is used to determine the elemental compositions of materials and to measure film thickness and composition. Electron Backscatter Diffraction (EBSD) is a great complement to the capabilities of our XRD services. While XRD can provide unparalleled information on phase ID, nanocrystalline grain size, thin film thickness and textures; the capabilities available by EBSD will provide spatial information, to help visualize the microstructure and add to a complete description of your crystalline samples.
At Eurofins EAG, our XRD team has collectively over 100 years of XRD expertise. We have a collaborative group coming from different backgrounds, industries and research specialties. With our recent addition of a Small Spot XRD tool along with our extensive instrument base, we offer a wide variety of analyses to tailor to our clients’ needs.
Contact us today to learn how we can help you on your next project.
In this webinar we will focus on Energy Dispersive X-ray Spectroscopy (EDS) and Scanning Electron Microscopy (SEM)
Contamination control and defect reduction are critical issues in the manufacturing process of compound semiconductor devices which can impact the performance of the end product. We can provide valuable insights to identify contaminants and characterize materials throughout the product lifecycle.
X-ray diffraction (XRD) is a powerful and versatile technique that can give detailed structural information about almost anything that is solid.
Vertical-cavity surface-emitting lasers, or VCSELs, play a major role in the consumer electronics 3D sensing industry.
To enable certain features and improve your experience with us, this site stores cookies on your computer. Please click Continue to provide your authorization and permanently remove this message.
To find out more, please see our privacy policy.