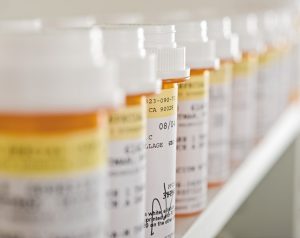
Using ICP-MS to Measure Elemental Compositions in Drug Products
ICP-MS is a multi-elemental bulk chemical analysis technique that can determine simultaneously up to 70 elements in a single sample.
Failure Analysis in Aerospace Advancements
Home » Failure Analysis in Aerospace Advancement
In 1903, the Wright brothers made history and presented the first aircraft capable of sustaining powered flight. Flight was made possible by the breakthrough invention of pilot operated wing-warping, crafted carefully by detailed research and incredible engineering.1 This success thus resulted in the birth of the aerospace industry.
From 1903 to modern times, the industry has expanded into commercial airplanes, spacecrafts, satellites, missiles and more, consequentially resulting in increasingly more complex electronic systems. Although these technological advancements are welcomed and necessary in today’s climate, the complexities that come with development present a variety of new problems including quality and safety standards.
EAG can assist with your failure analysis needs.
In the aerospace industry, electronics are subjected to extreme environmental variables such as wide and sudden swings in temperature, strong vibrations, lightning strikes, a multitude of forces acting in different directions simultaneously, severe pressure differentials, moisture intrusion, and ionizing radiation. This can lead to potential issues with control systems, impair aircraft sensors, hinder communication systems, and even compromise structural integrity. To help solve these problems, EAG’s failure analysis experts use advanced analytical tools and proven methodologies to achieve high quality results and reliable engineering assessment.
Some examples of techniques and tools we can use:
EAG is a certified partner (ISO 9001:2015, ISO 17025, ITAR compliant, MIL standards compliant) and offers services to assist with the innovation of new high-performance electronics, collaborate during the iterative efforts of increasing long term reliability, and when necessary, perform comprehensive investigations to identify elusive failure mechanisms. We support innovation at every phase of the product cycle.
Our engineers are knowledgeable and experienced in today’s advanced technologies and are well equipped to help assist in your investigative needs.
1 Culick, F. E. C. (2003). The Wright brothers: first aeronautical engineers and test pilots. AIAA journal, 41(6), 985-1006.
ICP-MS is a multi-elemental bulk chemical analysis technique that can determine simultaneously up to 70 elements in a single sample.
X-ray diffraction (XRD) is a powerful and versatile technique that can give detailed structural information about almost anything that is solid.
In this webinar we introduce the application of Electron Microscopy to Lithium Ion Batteries from Micron to Atomic Level
In this webinar we introduce Residual Gas Analysis (RGA), Evolved Gas Analysis (EGA), and Cumulative Helium Leak Detection (CHLD)
To enable certain features and improve your experience with us, this site stores cookies on your computer. Please click Continue to provide your authorization and permanently remove this message.
To find out more, please see our privacy policy.