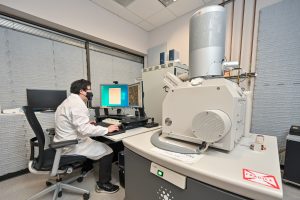
The Power of SEM-EDS in Imaging and Elemental Analysis
SEM equipped with EDS can capture detailed images and identify elements simultaneously on the surface of samples.
Home » Rare Earth Elements Aren’t So Rare After All
The term ‘rare earth elements’ (REEs) is a misnomer and better refers to the relatively rare ores REEs are extracted from; rare earth elements are all around us! In fact, the rarest of the rare earth elements, lutetium, is actually 200x more abundant than gold in terms of presence in the earth’s crust (Vonken, 2016).
While we physically see REEs far less than gold, they are commonly found in our electronics, in the cars we drive, and provide the variety of color in our LED lights among many more items we interact with daily.
REEs comprise the lanthanide series on the periodic table as well as Scandium (Sc) and Yttrium (Y). While Sc and Y differ in their electrical and magnetic properties, these elements appear together in nature and have similar chemical properties as REEs. REEs are sought out for their high electrical conductivity, their reducing powers, and their application in permanent magnets (Vonken, 2016).
A major application of RREs is in high-performance permanent magnets which are found in an array of technologies like smartphones, electric vehicles, wind turbines, computer hard drives, MRI machines, and even refrigerator doors. REEs are also used in nuclear reactor control rods (Guo et al., 2019) and in airplanes to strengthen alloys that are used in high temperature environments near the engine (Ahmed, 2003).
In 2021, the world mined 280,000 metric tons of REEs which is approximately 32 times as much as in the mid-1950s. Experts estimate that by 2040, this demand will increase a further seven times from what it is today (Fujita et al., 2022).
Unfortunately, the mining and processing of REEs is laborious and environmentally destructive as hundreds of thousands of gallons of wastewater result from purification efforts. As the demand for REEs rises, more effort is being put into recycling efforts. Currently, it is estimated that only about 1 percent of REEs in end-products get recycled (Wayman, 2023). Part of this lack of recycling is due to the low amounts of REEs used in individual products. For example, an entire hybrid
electric vehicle weighing almost two tons contains just over a kilogram of rare earth metal. While there is enough in a car for recycling to be advantageous, it is not always easy or cost effective to recycle lower amounts of REEs found in small consumer technologies (sometimes less than 1 mg). To meet rising demands for REEs and mitigate environmental impacts, the development of more cost-effective methods to isolate these materials needs to continue to be prioritized. Advances such as pyrometallurgical and hydrometallurgical recycling technologies are being developed (Takeda and Okabe, 2014). There is also a potential to separate REEs into easily removeable portions of EV batteries for easy recycling. Recycling will play a very important role in the future consumption of these metals and could account for up to one fourth of the need for REEs (Wayman, 2023).
Through our purity survey techniques, Eurofins EAG Laboratories (EAG) can conduct full scan trace analysis of REE materials. Glow Discharge Mass Spectrometry (GDMS) is a very sensitive and robust analytical tool for monitoring elemental compositions and impurities in materials down to trace and ultra-trace mass fraction levels. Inductively Coupled Plasma Mass Spectrometry (ICP-MS) is ideal for purity certification, cleaning validation and contamination identification for a broad range of materials and processes. Inductively Coupled Plasma Optical Emission Spectrometry (ICP-OES) is used to detect the presence of trace metals, playing a key role in tracking the performance of the cathode and understanding any deviations in battery performance. Lastly, Instrumental Gas Analysis (IGA) includes such methods as combustion, inert gas fusion, and hot extraction for determination of gas-forming elements (C, H, N, O, and S) present in solid materials from ppm to % levels. Contact us today to learn more about how our purity survey team can support your rare earth element analytical needs.
SEM equipped with EDS can capture detailed images and identify elements simultaneously on the surface of samples.
XRF is a non-destructive technique that is used to quantify the elemental composition of materials.
In this webinar we introduce Environmental chamber clean analysis that identifies contamination that can ruin your qualifications.
In this webinar we will focus on Rutherford Backscattering Spectrometry (RBS) which is a thin film analysis technique
To enable certain features and improve your experience with us, this site stores cookies on your computer. Please click Continue to provide your authorization and permanently remove this message.
To find out more, please see our privacy policy.