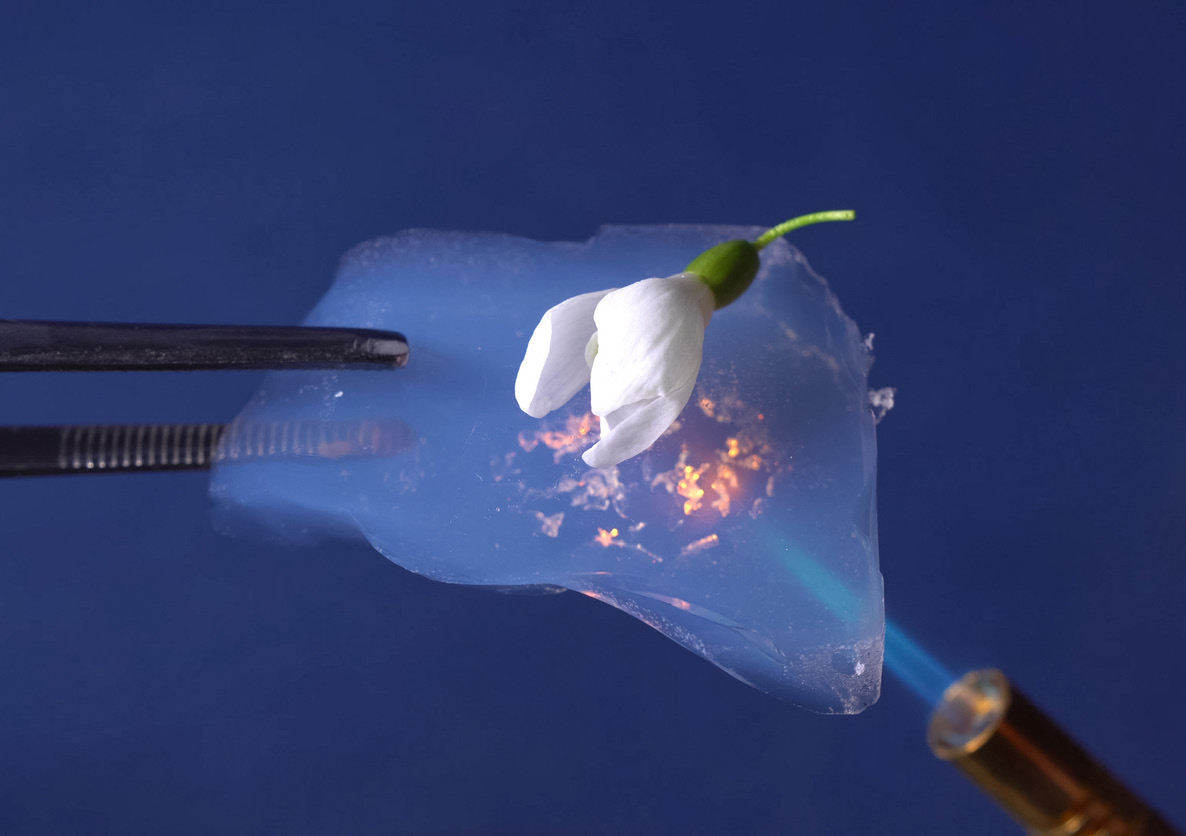
The Versatility and Usefulness of Aerogels
The Versatility and Usefulness of Aerogels Thermal resistance and its complement, thermal conductance, are fundamental concepts in thermodynamics, thermal engineering, and heat transfer. They describe the ability of a material