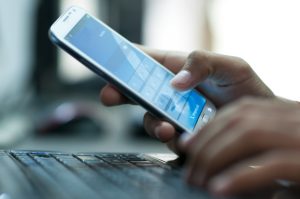
Navigating Consumer Electronics Development: Finished Products
As a trusted partner in the consumer electronics industry, we are ready to meet the evolving industry needs, advancing innovation and excellence.
To enable certain features and improve your experience with us, this site stores cookies on your computer. Please click Continue to provide your authorization and permanently remove this message.
To find out more, please see our privacy policy.