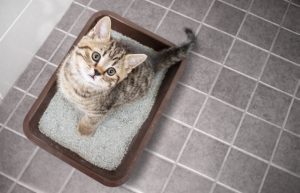
Diatomaceous Earth: A Marvel of Nature with Industrial Might
Diatomaceous Earth’s remarkable properties make it a versatile substance with a wide range of applications.
Home » Supplier Verification in Battery Manufacturing
With the continued growth and advancement in the world of batteries, there is a greater need to understand all the intricacies that are involved in battery manufacturing. Addressing and resolving materials issues associated with all stages of battery development, including supply chain, materials R&D, and failure analysis are critical and can affect the battery’s performance and life cycle. These tests require specialized analytical tools and expertise to better understand battery materials and the electrochemical processes that occur during battery cycling.
What do you do when the performance of your battery suddenly changes? Have there been recent changes to your manufacturing process? Have you recently changed materials supplier?
There is a long list of possibilities. One of the things that may be overlooked is the supplier. Do you have a supplier verification process? This is of utmost importance when you are relying on a material supplier. A minor change in the supplied material can potentially affect the reliability and performance of your product.
A customer wanted to verify a new supplier by comparing the quality and composition of 4 different batteries. This customer had worked with a supplier for years, providing a product with the specifications needed. Unfortunately, the supplier could no longer provide the same product and the customer had to find a new vendor. A combination of techniques was used for the evaluation, including CT scan, optical imaging, top-down and cross section SEM/EDS analysis of electrodes and separator, XRD of the cathode and GC-MS/LC-MS of the electrolyte. After our analysis, we determined that the new supplier’s product was close in comparison but was not identical.
At Eurofins EAG, we have specialized tools to confirm what a supplier is providing. For raw materials, we can inspect and verify the purity, as well as determine particle size and perform elemental analysis using techniques such as Glow Discharge Mass Spectrometry (GDMS), Inductively Coupled Plasma Mass Spectrometry (ICP-MS), Scanning Electron Microscopy (SEM) and X-Ray Diffraction (XRD). We can also test and compare composition in cathodes, anodes, electrolytes and separators using techniques such as X-ray Fluorescence (XRF), Fourier Transform Infrared Spectroscopy (FTIR), XRD and more.
Supplier verification can be critical to the long-term success of your product and business. At Eurofins EAG, our technical experts have many years of experience working with battery materials. We are your battery partner to bring your product to market faster and more efficiently. Contact us today to learn how we can help.
Diatomaceous Earth’s remarkable properties make it a versatile substance with a wide range of applications.
Solids fall under two main categories: amorphous and crystalline. These two types of solids have different properties that may be more beneficial for certain products or applications.
A company was investigating environmental stress cracking of polycarbonate components used in a conveyor device that was sanitized.
Electrochromic Glass, also known as smart glass, is a newer technology which allows users to turn glass opaque when needed, and clear when not.
To enable certain features and improve your experience with us, this site stores cookies on your computer. Please click Continue to provide your authorization and permanently remove this message.
To find out more, please see our privacy policy.