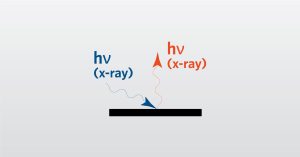
XRF Webinar
In this webinar we introduce X-ray Fluorescence Spectroscopy (XRF) which is a analytical technique used for elemental analysis of materials.
Home » Understanding Energy Density in Batteries
From cell phones to electric vehicles (EV), lithium-ion batteries are part of our daily lives. With the ever-increasing demands for batteries in automotive, energy storage and consumer electronics, there also comes a greater need for improved performance and safety. There is still so much to learn about batteries, including challenges such as energy density, cycle life, fast charge, and safety. In this blog, we’ll be focusing on energy density.
Have you ever wished that your phone doesn’t run out of battery in the middle of a call or wanted to drive more miles before having to charge your EV? Have you ever wondered why your smart watch cannot be more sleek-looking or why EVs are more expensive than gasoline cars? At the core of these questions, there is an energy density problem of batteries. In products like smart watches or smart phones, the battery is the largest component behind the display. In typical EVs, the cost of the battery pack makes about 40% of the total vehicle cost. Only if we can increase the energy densities of today’s batteries, we can use our phones or EVs longer between charges, we can have more sleek or smaller devices, and we can make EVs more affordable.
A ton of research groups and innovative companies around the world are actively working to improve batteries’ energy densities using various approaches. Obvious one is to minimize the amount of non-active materials inside of a battery that don’t contribute to storing energy directly such as casings, current collecting metal foils and polymer separators; and there has been significant improvement in these efforts over the past two decades.
Increasing the amount of energy that active materials can hold is the other approach. For cathode active materials, it is the common view that today’s ubiquitous lithium-transition metal oxides don’t have much room left for further improvement, while sulfur-based cathode will be able to make a leap in energy density once the challenges associated with the dissolution of polysulfide are overcome. For the anode active materials, silicon and lithium are known to be able to store about 10 times the capacity than that of the graphite but have not been used as anodes in products due to instabilities such as pulverization, dendrite growth, and unstable solid-electrolyte interphase (SEI) layer, leading to eventual capacity loss. Various approaches to confine or accommodate these instabilities are being demonstrated along with improved energy densities at the commercial scale.
At Eurofins EAG, our industry leading materials and advanced microscopy services can help with research and investigations needed for battery manufacturing and failure analysis down to the nanoscale at which the engineering of the materials to improve the energy density actually happens. With our new battery lab, we have capabilities to handle air-free transfer for our samples along with a wide range of specialized techniques such as Plasma FIB, Cryo FIB and Cryo TEM.
Our scientists can help you understand the chemistry and morphology of nano-engineered materials and SEI layers using analytical techniques such as SEM, TEM, XPS, Auger, NMR, FTIR and TOF-SIMS. Our trace elemental services can determine the purity of raw materials such as graphite, silicon, and lithium.
As the battery industry continues to evolve, Eurofins EAG Laboratories is your partner to bring your product to market faster and more efficiently. Contact us today to learn how we can help you to better understand your battery materials and processes.
In this webinar we introduce X-ray Fluorescence Spectroscopy (XRF) which is a analytical technique used for elemental analysis of materials.
In this webinar we introduce latch-up testing which is relevant for CMOS devices with high static power dissipation.
Aerospace and defense government suppliers can have confidence in EAG’s credibility in providing accurate and high-quality testing services.
Contamination control and defect reduction are critical issues in the manufacturing process of compound semiconductor devices which can impact the performance of the end product. We can provide valuable insights to identify contaminants and characterize materials throughout the product lifecycle.
To enable certain features and improve your experience with us, this site stores cookies on your computer. Please click Continue to provide your authorization and permanently remove this message.
To find out more, please see our privacy policy.