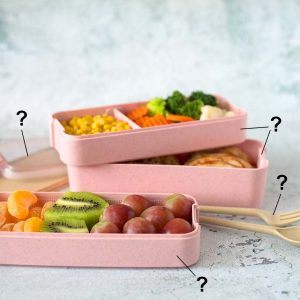
FTIR and Raman – Composition and Contamination Analysis
FTIR and Raman are spectroscopy techniques that provide molecular information from various types of materials.
Home » Lithium Ore and Concentrates for Battery Production and Beyond
With the increased focus on renewable energy to counteract climate change and other environmental issues related to fossil fuel consumption, consumers are becoming ever more aware of lithium and where it comes from. While lithium is used in a lot of everyday applications, the rapidly growing Electric Vehicle (EV) market is currently driving demand. According to the U.S. Geological Survey, excluding U.S. production, worldwide lithium production in 2022 increased by 21% to approximately 130,000 tons from 107,000 tons in 2021. This is in response to the strong demand from the lithium-ion battery market and increased prices of lithium. Further, global consumption of lithium in 2022 was estimated to be 134,000 tons, a 41% increase from 95,000 tons in 2021. Construction of lithium battery recycling plants has also increased at a rapid pace. As of November 2022, about 44 companies in Canada in the United States and 47 companies in Europe recycled lithium batteries or planned to
do so.1 (Brian W. Jaskula, 2023). Eurofins EAG Laboratories stands ready to assist in the analysis of lithium-ion batteries from the raw material supply chain through to the finished product and eventual recycling.
Lithium ore, also known as hard-rock lithium, is derived from mining and is one of the major raw material sources for lithium production for industrial applications – the other source is lithium brines. Hard-rock lithium deposits are found in countries like Australia, Brazil, Canada, Ireland, Finland, Democratic Republic of Congo, and Zimbabwe, among others. The most important minerals for lithium mining are spodumene (Li2O, Al2O3·4SiO2) and petalite (Li2O, Al2O3·8SiO2). Both minerals occur in granitic pegmatites, a type of igneous rock characterized by its coarse texture and mineralogical composition dominated by quartz, feldspar, and mica. Lithium is perhaps best known for its role in advanced battery production, as well as having long-established applications in ceramics, metallurgy, and medicine.
Processing hard-rock lithium into concentrates for industrial applications can yield either lithium hydroxide (LiOH) or lithium carbonate (Li2CO3). Lithium carbonate can be either a precursor compound to lithium hydroxide or an end-product. As an end-product, lithium carbonate is widely used in ceramics and glassware, cement, industrial greases, aluminum production, and, at pharmaceutical-grade purity, as a maintenance treatment for bipolar and major depressive disorders. As an intermediate product for battery production, lithium carbonate is subjected to additional processing to yield lithium hydroxide.
Lithium carbonate production from ore entails initial crushing and roasting, cooling, and milling, followed by roasting with sulfuric acid to achieve acid leaching and yield lithium sulfate. Lime (calcium carbonate) or other calcium compounds are then added to remove magnesium derived from the spodumene ore, followed by the addition of soda ash (sodium carbonate) to induce precipitation of lithium carbonate from the lithium sulfate solution. By adding hydrated lime (calcium hydroxide) to lithium carbonate, the lithium ions will exchange places with the calcium in the lime (known as a salt metathesis reaction) to yield lithium hydroxide and a calcium carbonate residue. Lithium hydroxide is typically used in high-performance batteries, such as those used in electric vehicles, where purity is important for performance and safety reasons.
While commercial laboratories primarily focused on the extractive industries offer testing services for lithium ores like spodumene and petalite, Eurofins EAG Laboratories is uniquely situated to provide purity testing of lithium carbonate or hydroxide concentrates for the most demanding applications like electric vehicle batteries. “Battery grade” purity standards vary slightly from manufacturer to manufacturer, but typically lithium carbonate of > 99.5% purity and lithium hydroxide of > 99% purity are considered suitable for battery precursors. The Purity Survey business line of EAG Laboratories has a long record of serving industries like aerospace, defense, and semiconductor manufacturing that have extremely stringent purity requirements. By offering a suite of complementary techniques such as Glow Discharge Mass Spectrometry (GDMS), Inductively Coupled Plasma-Mass Spectrometry (ICP-MS), Inductively Coupled Plasma-Optical Emission Spectroscopy (ICP-OES), Laser Ablation-Inductively Coupled Plasma-Mass Spectrometry (LA-ICP-MS), and Laser Induced Breakdown Spectroscopy (LIBS), EAG can be a one-stop shop for purity analysis of lithium concentrates and other precursors used in advanced battery production. Contact us today to learn more about how we can partner to address your needs.
Brian W. Jaskula, M. C. (2023). 2023 Lithium Mineral Commodity Summary. U.S. Geological Survey. National Minerals Information Center. Retrieved from https://www.usgs.gov/centers/national-minerals-information-center/lithium-statistics-and-information
FTIR and Raman are spectroscopy techniques that provide molecular information from various types of materials.
It’s cool to know that some of the analytical techniques available at EAG, such as SEM and XRD, are being used to analyze a sample from space! How awesome is that?
Solids fall under two main categories: amorphous and crystalline. These two types of solids have different properties that may be more beneficial for certain products or applications.
EAG Laboratories provides clients with answers to these questions and more with testing support for every stage of the supply chain.
To enable certain features and improve your experience with us, this site stores cookies on your computer. Please click Continue to provide your authorization and permanently remove this message.
To find out more, please see our privacy policy.