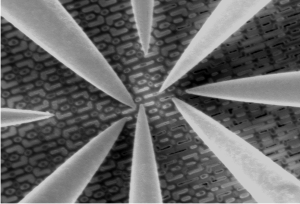
Nanoprobing in the Evolving World of Electronic Systems
Nanoprobing is crucial for understanding advanced semiconductor devices, finding faults, and conducting thorough failure analysis.
Home » Surface Chemistry and Composition in Battery Manufacturing
From cell phones to electric vehicles, lithium-ion batteries are part of our daily lives. We rely on their performance and safety to power the majority of consumer electronics. With increasing demands for higher battery performance and improved safety, a better understanding of the factors affecting performance, life cycle and possible failure mechanisms is essential.
In our blog, Understanding Lithium-Ion Batteries and Why They Fail, we talk about how EAG assists in achieving clean and consistent manufacturing using our trace elemental analysis techniques such as Glow Discharge Mass Spectrometry (GDMS), Inductively Coupled Plasma Mass Spectrometry (ICP-MS), and Inductively Coupled Plasma Optimal Emission Spectroscopy (ICP-OES). In this blog, we’ll be focusing on a few of our materials characterization techniques that can help identify surface chemistry and composition of the materials used to develop new batteries.
Measuring the chemical state of the battery components such as the cathode, anode, separator, electrolyte, contact layers and additives, at various stages of cycling, provides vital information about the electrochemical processes that occur during battery use. EAG offers elemental and molecular analyses using a number of different analytical tools to address this need.
The surface chemistry of an electrode can change after battery cycling. X-ray Photoelectron Spectroscopy (XPS) is a commonly used technique for this type of investigation. XPS can help look at comparisons between control and treated samples.
Time-of-Flight Secondary Ion Mass Spectrometry (TOF-SIMS) has the unique ability of analyzing both organic and inorganic components. This is helpful in a full investigation of decomposition, presence of impurities, or any other surface changes during cycling.
Auger Electron Spectroscopy allows elemental analysis using an electron beam focused down to ~10-20 nm, enabling specific regions of interest on electrode particles to be analyzed. This surface analysis technique can show the presence of species characteristic of the anode, cathode and electrolyte.
A customer discovered a change in the surface of their cathode after cycling. TOF-SIMS was used to investigate particles found on the surface. Molecular species of interest were identified on the surface of a cathode that did not originate there. Our TOF-SIMS experts were able to provide our customers with a better understanding of the lateral chemical distribution of species of interest at various stages of cycling.
These are just a few of our materials characterization techniques that can help to better understand battery components and improve performance, reliability and safety. At Eurofins EAG, our scientists have helped the battery industry with a wide range of materials characterization services for supply chain, materials R&D, and failure analysis. We work closely with our clients to help identify and solve problems. As the battery industry continues to evolve, Eurofins EAG Laboratories is your partner to bring your product to market faster and more efficiently.
Contact us today to learn how we can help you to better understand your battery materials and processes.
Nanoprobing is crucial for understanding advanced semiconductor devices, finding faults, and conducting thorough failure analysis.
Developing a reliable product has many challenges due to the desire for increased capability, reduction in formfactor, and managing the supply chain.
XRD analysis can be used on many scientific and technology-based applications where you may want to identify the crystalline material in a very small area or volume, such as glass defects or inclusions, integrated circuits, LEDs and more.
In this webinar we introduce failure analysis of ICs and other components in the product development cycle and for improving current products
To enable certain features and improve your experience with us, this site stores cookies on your computer. Please click Continue to provide your authorization and permanently remove this message.
To find out more, please see our privacy policy.